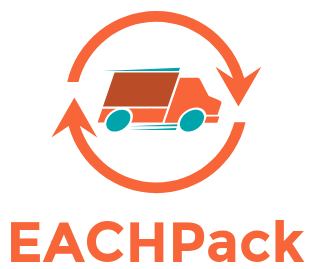
IT+Robotics as part of EACHPack, a component of the Trinity EU Project
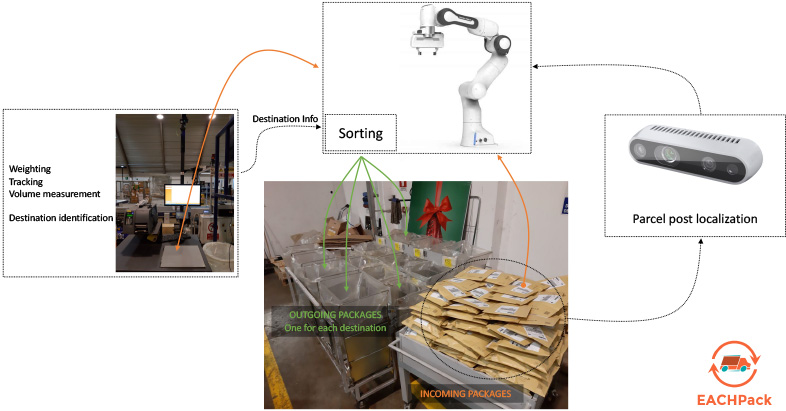
NEED
The growth of e-commerce is leading to the explosion of small parcel post shipments, at the same time increasing the number of shipments while reducing the average size of the sent packages. Local facilities of express couriers (also called local branches, or delivery facilities in this document), that have in charge both first reception of parcel posts and their dispatch to the final destinations, are facing new important challenges in managing these market changes. Handling small parcel posts (e.g., under 5 kg) requires a lot of tiring human work and several repetitive actions, while the profit margin for each managed package is constantly decreasing. The EACHPack project, the acronym for End-to-end AutomatiC Handling of small Packages, aims to propose a demonstration of a new robotic system capable of carrying out the whole handling process of incoming parcel posts in a fully autonomous way. Furthermore, the proposed system will support collaborative tasks, i.e., it should enable to safely operate with human operators in the middle. A demonstrator of the proposed system will be installed on a real express courier delivery facility already used to test new technologies.
APPROACH
With the EACHPack project, we aim to provide within 3 years a complete robotized system to small and medium delivery structures, capable of performing the incoming parcel posts management process in an end-to-end fashion. Such a process requires to grasp packages from one or more containers, recognize packages information to manage the tracking process, measure their weight and volume, and place them on specific outgoing containers. In incoming parcel posts handling, operators are subjected to stressful 3-4 hours work shifts, in which they arrive to handle up to 400 packages per hour. Actually, the cycle time, i.e. the system speed, represents the main challenge that the EACHPack project will face in the demonstrator development. Safety for cooperating humans and the final cost of the provided system represent are other essential requirements to satisfy.
BENEFIT
The results of this project will serve as the backbone of a family of new products and services that the EACHPack consortium aims to develop and implement in real logistic applications within the next 3 years. Products include the developed software, sensors, and actuators, services include the integration with the existing production lines and the assistance. The number of small delivery facilities potentially interested in the proposed system is rather high (around 250 only in Italy). On the other hand, very rarely such facilities use robotic cells to automate the handling of the packages, due to the lack of end-to-end solutions able to effectively perform the whole process. As EACHPack consortium, we expect to sell 15 complete solutions within 3 years in Italy, with an expansion to the European market with other 50 systems sold within 5 years.

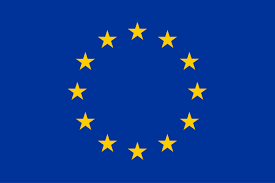